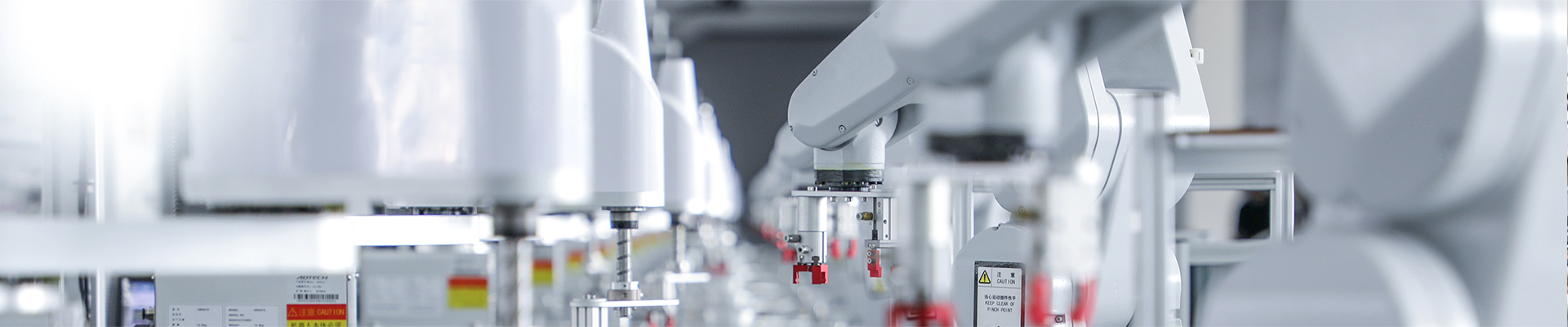
What are the material science considerations for "Cable Stringing Accessories" to ensure durability and performance in diverse global environments?
2025-07-20Material science is a critical consideration for "Cable Stringing Accessories" due to the extreme mechanical stresses, diverse environmental conditions, and long service life expected of these components globally. The choice of materials directly impacts durability, performance, and safety.
Key material considerations include:
-
High-Strength & Lightweight Alloys:
-
Aluminum Alloys: Widely used for stringing block sheaves, frames, and some grips due to their excellent strength-to-weight ratio. Alloys are chosen for specific properties like resistance to deformation under high load, corrosion resistance, and good machinability.
-
Heat-Treated Steel Alloys: Used for components requiring maximum strength and wear resistance, such as pins, shafts, load-bearing frames, and critical parts of pulling swivels and heavy-duty clamps. Heat treatment processes (e.g., quenching and tempering) enhance their hardness and toughness.
-
-
Corrosion Resistance:
-
Galvanization: Steel components are often hot-dip galvanized or electro-galvanized to provide a sacrificial zinc coating that protects against rust and corrosion in humid, coastal, or industrial environments.
-
Stainless Steel: Used for fasteners, springs, and components exposed to highly corrosive conditions (e.g., marine environments, chemical plants) due to its inherent corrosion resistance.
-
-
Wear-Resistant & Low-Friction Polymers/Composites:
-
MC Nylon (Cast Nylon), Polyurethane, HDPE: Increasingly used for sheave liners in stringing blocks (especially for sensitive conductors like OPGW or covered cables). These materials offer:
-
Excellent Abrasion Resistance: Withstand continuous rubbing from conductors.
-
Low Coefficient of Friction: Significantly reduce pulling friction and prevent damage to conductor jackets.
-
Impact Resistance: Absorb shocks without deforming.
-
Chemical Resistance: Stand up to lubricants, pollutants, and various environmental chemicals.
-
-
-
Elastomers (Rubbers/Synthetics):
-
Neoprene/EPDM: Used for seals in bearings (e.g., in swivels) to protect against dust, moisture, and contaminants, extending bearing life. Also used in anti-vibration dampers for their elastic and energy-absorbing properties.
-
-
UV Stability: For accessories permanently exposed to sunlight (e.g., some types of spacers, helical dampers), materials must be UV-stabilized to prevent degradation, embrittlement, and color fading over time.
-
Temperature Performance: Materials must maintain their mechanical properties and dimensional stability across the expected operating temperature range, from extreme cold to high heat, without becoming brittle or softening.
-
Dielectric Properties (for Insulated Accessories): For tools used near live lines or for insulating components (e.g., hot sticks, temporary cover-ups), materials with high dielectric strength and good tracking resistance (e.g., fiberglass, specialized polymers) are crucial.
By carefully selecting and processing these advanced materials, manufacturers ensure that "Cable Stringing Accessories" provide the necessary strength, durability, and protective qualities to perform reliably in the demanding environments of global overhead transmission line construction.